Do you know what a Ceramic Wafer Chuck is?
When it comes to the manufacture of semiconductors and microelectronics, accuracy, stability, and the qualities of the materials all play critical roles in ensuring that the production processes are both efficient and of high quality. The ceramic wafer chuck is an essential component that exhibits these characteristics and provides an example of them. In the field of high technology, what precisely is a ceramic wafer chuck, and why is it considered to be of such critical importance?Immerse yourself in the complexities of ceramic wafer chucks by investigating their functions, benefits, applications, and the technologies that led to their invention.
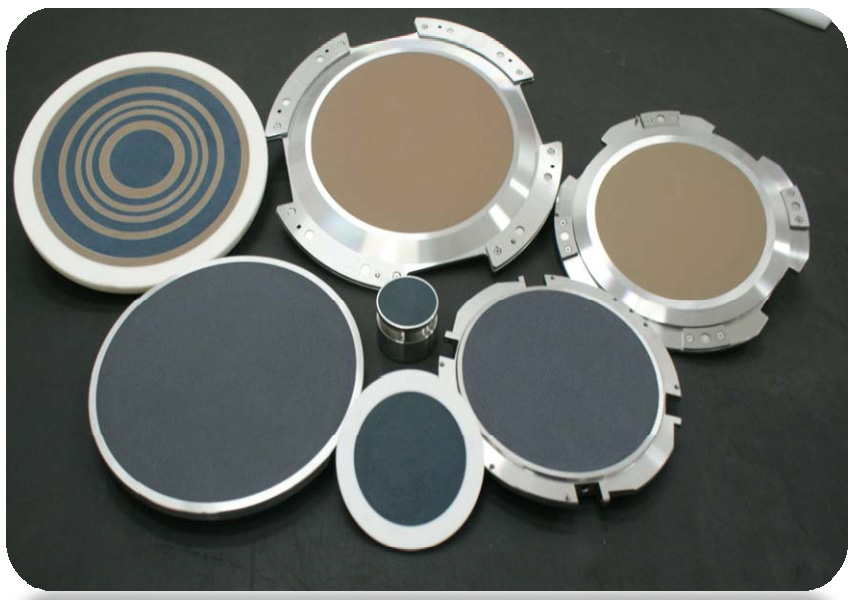
When it comes to the fundamentals, what exactly is a Wafer Chuck?
It is a device that is used to secure and support semiconductor wafers throughout different production processes. A wafer chuck, which is also known as a wafer holder, is another name for this device. Photolithography, etching, ion implantation, and chemical vapour deposition (CVD) are only few of the procedures that fall under this category. The chuck guarantees that the wafer will stay stable and properly positioned during the processing, which enables processing that is exact and produces high-quality results.
Ceramics play an important role in wafer chucks."
Ceramic materials, notably those based on aluminum oxide (alumina), silicon carbide, and aluminum nitride, are highly prized in wafer chucks because to the remarkable qualities that characterize these materials. In comparison to other materials, such as metals and polymers, ceramics have a number of benefits, including the following:
Ceramics have a high thermal stability, which means that they are able to tolerate high temperatures without deforming. This makes them an excellent choice for procedures that entail high heat.
Low Thermal Expansion Ceramics are able to keep their dimensional stability because to their low thermal expansion coefficient, which is an essential quality for materials used in precision production.
Chemical Inertness: Ceramics are resistant to corrosion and chemical reactions, which is required in the hostile conditions of semiconductor production. Ceramics also meet the requirements for chemical inertness.
Insulation from Electrical Current Ceramics are good electrical insulators, which reduces the likelihood of undesirable electrical interactions occurring during wafer manufacturing.
In terms of mechanical strength and hardness, ceramics are very tough and long-lasting, which guarantees their lifespan as well as their resistance to wear and damage.
Varieties of Wafer Chucks Made of Ceramic
There is a wide variety of designs available for ceramic wafer chucks, each of which is suited to particular applications and needs. The following are the major types:
(ESCs) stands for electrostatic Chucks.
The wafer is held in position by electrostatic chucks by the application of an electrostatic force. Especially helpful in vacuum situations, where mechanical clamping would be impossible, they are known for their effectiveness. ESCs may be broken down into two primary categories:
For the purpose of producing an electrostatic field, the Coulomb type makes use of direct current (DC) voltage source.
In order to generate a more powerful holding force, the Johnsen-Rahbek type makes use of a combination of direct current voltage and surface roughness.
Chucks for vacuuming
Vacuum chucks are able to firmly keep the wafer in place because they generate a suction force by using a vacuum. It is usual practice to use them in procedures in which the wafer must be held tightly without the possibility of any harm being caused by clamping devices.
Chucks that are mechanical
The wafer is held in place by mechanical chucks by the use of physical clamps or other devices. In spite of the fact that they are not as often employed in the production of high-precision semiconductors, they are nevertheless used in some applications.
Ceramic wafer chucks have a variety of applications.
Ceramic wafer chucks are vital in a wide variety of high-tech applications because to their outstanding characteristics and adaptability. These applications include the following:
Manufacturing of Semiconductor Devices
Precision and consistency are of the utmost importance in the manufacture of semiconductors. Ceramic wafer chucks provide the essential support throughout the operations of photolithography, etching, and deposition, which helps to ensure that microchips and other semiconductor devices are of a high quality.
The Fabrication of MEMS
Microelectromechanical systems, often known as MEMS, need processing and handling that is very careful. Ceramic chucks provide the stability and accuracy that are necessary for the production of these very complicated and minute devices.
Manufacturing of Solar Cells
Photovoltaic cells are manufactured using corrosive chemicals and high temperatures throughout the manufacturing process. Solar cells are able to maintain their efficiency and durability because to ceramic wafer chucks, which are able to tolerate these extreme circumstances.
The Production of LEDs
It is necessary to conduct precise processing on light-emitting diodes (LEDs) in order to obtain maximum performance. During the process of fabricating LED wafers, ceramic chucks provide the levels of precision and stability that are required.
Ceramic Wafer Chucks Offer a Number of Benefits
Wafer chucks made of ceramic provide a number of specific benefits, which contribute to their extensive usage in the microelectronics industry. These advantages include the following:
Precision and Stability: Ceramics are known for their dimensional stability and minimal thermal expansion, which ensures that the wafer will stay properly aligned during the production process. This results in greater yields and fewer faults.
Ceramics because of their hardness and chemical resistance make these chucks very robust. As a result, they reduce the frequency with which they need to be replaced and minimize the amount of time that they undergo downtime.
Ceramics are able to withstand the high temperatures that are often needed in the production of semiconductors without deteriorating or deforming despite the high temperatures.
Electrical Insulation Ceramics have the ability to avoid electrical interference due to their insulating qualities, which is essential in operations that involve sensitive electronic components.
Ceramics have a chemical resistance because of their inert character, which shields them from the corrosive chemicals that are employed in the different methods of manufacture. This ensures that ceramics are long-lasting and reliable.
Creating Ceramic Wafer Chucks via Manufacturing
When it comes to manufacturing ceramic wafer chucks, there are a few essential measures that must be taken in order to guarantee that the finished product is up to the standards of the semiconductor industry. Included in these steps are:
The Selection of Materials and Their Preparation
Selecting the appropriate ceramic material is the first stage in the process. Due to the excellent qualities that they possess, high-purity alumina, silicon carbide, and aluminum nitride are often selected. In order to obtain the necessary particle size and eliminate any impurities, the raw materials are subjected to a meticulous processing procedure.
The process of forming and sintering
Techniques like as pressing, extrusion, and injection molding are used in order to shape the ceramic powder that has been manufactured into the required shape. The item that has been created is then subjected to high temperatures in order to acquire the required density and mechanical strength that is required.
Machining and Surface Finishing Operations
Immediately after the sintering process, the ceramic chuck is subjected to precision machining in order to obtain the requisite surface smoothness and dimensions perfectly. Grinding, lapping, and polishing are some of the techniques that are used in order to get a smooth and flat surface that is capable of holding the wafer firmly.
Regulation of Quality
A comprehensive set of quality control procedures has been implemented to guarantee that every ceramic wafer chuck satisfies the stringent requirements that are necessary for the production of semiconductors. Dimensional inspections, surface roughness measures, and performance evaluations are all included in this.
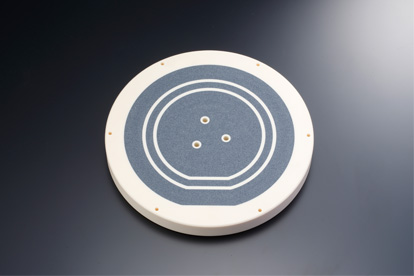
Final Thoughts
Ceramic wafer chucks are an essential component in the semiconductor and microelectronics industries. They provide the stability, accuracy, and durability that are necessary for the production of high-quality goods. Because of their exceptional qualities, which include high thermal stability, minimal thermal expansion, chemical inertness, electrical insulation, and mechanical strength, they are an excellent option for a wide range of applications.
By gaining an understanding of the benefits and uses of ceramic wafer chucks, one may better appreciate the significance of these tools in contemporary technology. Ceramic wafer chucks will continue to play an increasingly important role in assuring the quality and efficiency of semiconductor production as the demand for electronic devices that are both more powerful and smaller continues to increase.
We have a more profound appreciation for the technology that supports the devices that we depend on on a daily basis when we investigate the complexities of ceramic wafer chucks, which range from their fundamental functions to the comprehensive manufacturing procedures that they undergo. Ceramic wafer chucks are an essential component in the advancement of the capabilities of the microelectronics sector. This is true whether the semiconductor fabrication, MEMS production, solar cell manufacturing, or LED fabrication procedures are being carried out.